Ski Bible
The Injection
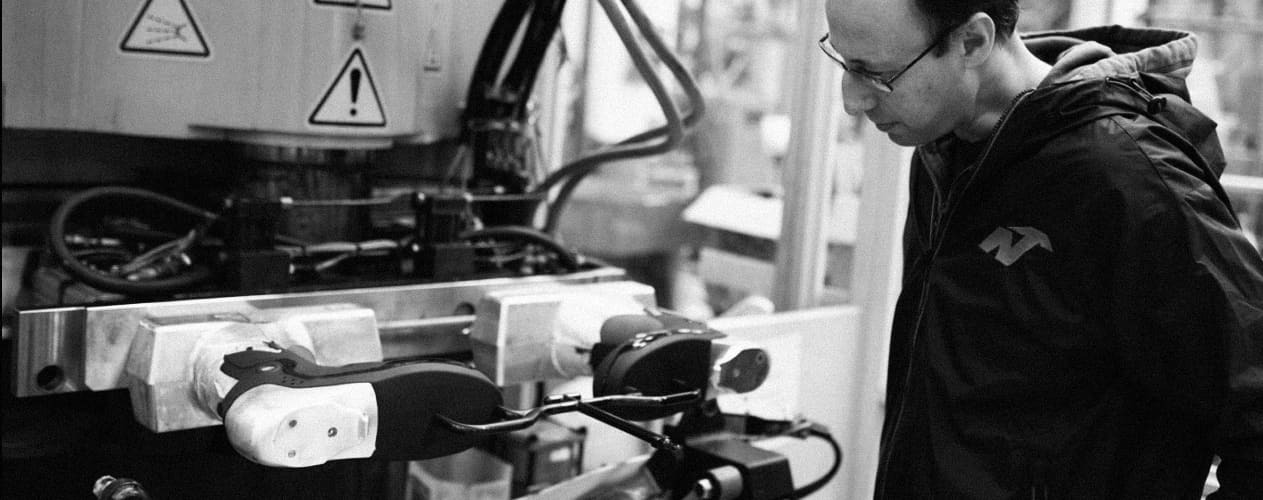
The second chapter of this saga is about one main topic of the productive process of a ski boot: the injection. Other than being a very delicate step in the creation of the ski boot, it also represents the synthesis of lots of different intrinsic qualities of the product, that inevitably determine its value.
The injection printing technology is an industrial production process, that uses the presses while melting the plastic material and pouring it into a mold. Then, the compound, made of small grainy parts, is poured into a hopper, that directs the compound along the heater. In this phase takes place the plastics fusion process, which later will be inserted in the specific cavity to fill up the mold. Once it’s become solid, the plastic takes the desired shape. A first step requiring maximum precision, extremely accurate evaluation, and technical skills. Skiing, one of the sports mostly dependent on external situations, must take into consideration many different variables, that are reflected on all production cycles of the equipment.
The temperature excursions and climate conditions to which ski boots are subject- both factors that influence the selection of plastics to be used - must respond to certain criteria and have very specific features. Each ski boot has its own special stiffness (flex index), which must always remain unchanged, dealing with cold winter temperatures. For this reason, the large family of plastic materials is carefully analyzed by our R&D department before choosing the finest and best performing materials for ì each ski boot.
The careful selection of the best polymers, together with the refinement of the injection technique, set the base to create different constructions of the shell, specifically studied to meet the needs of countless skiers.
specifically studied to meet the needs of countless skiers. To start clarifying this innovative process adopted by Nordica,
it is, first of all, important to divide the shell in two greater categories:
mono-injected and bi-injected.
Mono-injection
Dobermann Gp Vs The Cruise
A practical example highlighting the complexity of the same development technique is the difference between the Dobermann GP and the Cruise. The Dobermann GP is a ski boot inspire by the racing world, of which the aesthetic reminds of the models used by our athletes in the World Cup, with a declination of more versatile piste style. In fact, the entire family was created for expert skiers, committed to compete, who want a more dynamic and though set-up. The sole of the foot is 98mm wide- usually considered low volume- allowing extreme precision in each phase of the turn. Moreover, it’s provided with coherent and efficient technologies, also racing-oriented, designed for better performance. Among these, there’s the Full Motion Pivot, a screwing system that allows the skier to regulate and turn the cuff of just a few millimeters; and the Power Strap of 60mm, of which the elasticity and resistance facilitate the progressive distribution of weight when at high speed.
On the other hand, the Cruise, regardless of its mono-injected shell, is a ski boot line specifically designed for a completely different target compared to the racing enthusiast choosing the Dobermann GP. The width of the sole of the foot-104mm- already shows a distinctive trait of the Cruise family: total comfort. Without compromising the performance and overall skiing result, the plastic thickness of the Cruise is slightly lower, and its technologies primarily focus on comfort. The Adjustable Cuff Profile (ACP) is the proof of it, a simple system studied to increase the circumference of the cuff of the ski boot. Thanks to a double screw placed in the posterior part of the shell, the skier can customize the fitting, finding more comfort and a more natural posture when on skis.
The structural differences between the two families, the Dobermann GP and the Cruise, two very different, if not diametrically opposite, products can be the result of one single process.
Bi-iniezione
The continuous pursuit of perfection, that has always defined our journey, led us to the discovery of innovations that made our products authentic icons in the history of the ski boot. The natural evolution of the mono-injection represents the attempt to use more plastic densities, combining stiffer materials with some softer ones, adapting to the most sensitive and delicate part of the foot. The introduction of the bi-injection construction technique was an important step towards the productive process, as well as becoming the main distinctive feature of the Machine products family. Also in this case, our technicians used their knowledge and skills to improve even more all the already existing technical procedures.
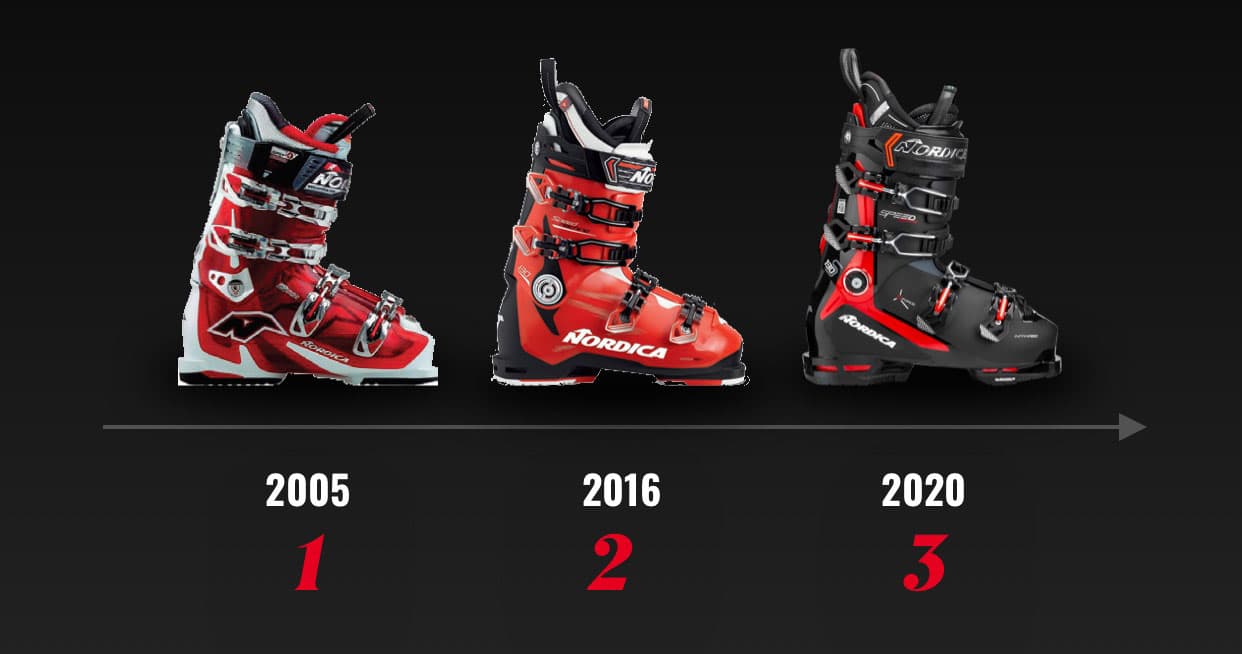
From The Og Speedmachine To The New Speedmachine: Two Generations Compared
The fil rouge that runs through the entire story of the bi-injection of Nordica can be associated to the iconic model of our collection: the Speedmachine (100 mm). Although it was not our the first bi-injection model, the Speedmachine has been so successful also thanks to this production technique, improved and perfected over the years. The highlight of the process is the innovative hybrid shell, made of a more rigid material, essential to the accurate transmission of pulses, and a softer one, that can wrap around the foot in the areas requiring more comfort. Benefitting from the same process, the Machine Family is now complete with the Promachine (98mm) and the Sportmachine (102mm).
This year the cyclical story of the Machine Family starts with its firstborn, thanks to a full technological and innovative reinterpretation. The third generation introduces a bi-injected structure, redesigned based on very specific goals: harmony, performance, control and comfort. The Speedmachine 3.0 can be considered a true revolution, inspired by the number three, symbol of perfection and numerous schools of thought.
Three, exactly just like the polyurethanes used for the construction of the shell. The newest addition is about the two most important components for performance on snow, meaning a hard stiff plastic and an intermediate-flexible one.
From simply assembling, we went to a synergic integration, made possible thanks to the Honeycomb technology, an incredibly innovative shell, as the name itself suggests, with a honeycomb structure that combines different plastics creating a perfect blend. The third insert is an even softer part, placed on the instep, a very sensitive part when stepping in and out of the boot.
The analysis and the comparison between these categories help us understand the ski boot’s evolutionary steps during its creation process, from raw grainy compound to shiny shell.
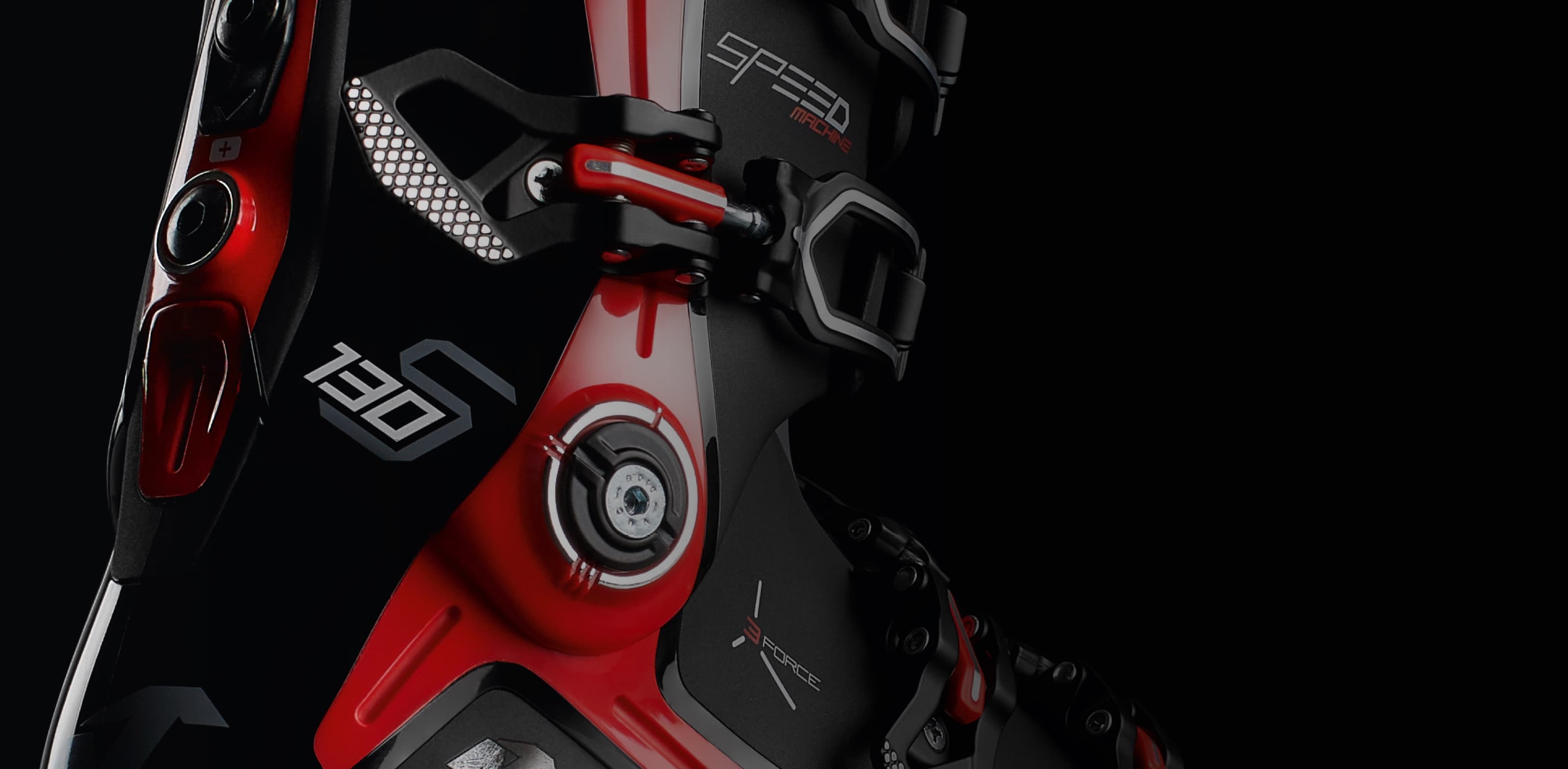
The analysis and the comparison between these categories help us understand the ski boot’s evolutionary steps during its creation process, from raw grainy compound to shiny shell.
The engineering nature of these products does not limit only to the construction of the external shell, but also all other components. Now, you just need to hold on until next chapter, where we will explore other technical topics to feed your craving for more information.